|
Post by Ryan_M on Nov 22, 2014 20:33:09 GMT -5
I switched to 0.035 flux core which was a great idea but didn't help. In fact, it was worse. Not only was I blowing holes I was also blowing dust and slag everywhere. Even on new clean metal it was rougher than what I was doing with the gas. So I switched back to gas but this time tried 0.030 instead of the 0.025 wire I had last time.
Not sure if this tub is just too tender or what but I so much as touch it with a welder and it burns like tissue paper. If I can find any way to patch this hole in the wheel well (which has now grown to completely destroy one of those highly visible ridges) I'm ready to blast a coat of paint on it and call it good - rotted toolbox and all.
|
|
Deleted
Deleted Member
Posts: 0
|
Post by Deleted on Nov 22, 2014 22:39:53 GMT -5
Here is what I would do!. .025 wire, gas, if your too hot INCREASE wire speed, this will cool the weld, when you get to the point it piles up the wire it is to fast, so back it off a touch. IMHO your wire speed is to slow. Think of it this way, to increase penetration you want to slow the wire and increase heat. To decrease penetration (this is what you want!) speed up the wire and decrease heat!. Lee 
|
|
|
Post by Haines Garage on Nov 22, 2014 23:41:53 GMT -5
Here is what I would do!. .025 wire, gas, if your too hot INCREASE wire speed, this will cool the weld, when you get to the point it piles up the wire it is to fast, so back it off a touch. IMHO your wire speed is to slow. Think of it this way, to increase penetration you want to slow the wire and increase heat. To decrease penetration (this is what you want!) speed up the wire and decrease heat!. Lee  Great explaination there. While we are talking about wire, reasons for the sizes?
|
|
|
Post by Ryan_M on Nov 23, 2014 6:29:38 GMT -5
Thanks Lee. I have thought about it that way and did increase wire speed to try and compensate for too much heat but I have not found that "sweet spot". I either burn holes immediately because it's too hot or, if I increase wire speed, it feeds so fast the arc "pops" and blows a bigger hole. After all of this advice I've read I can pretty much recite "exactly" what I should be doing but when it comes time to actually do it it's a trainwreck. Well today's a new day and that means a new pot of coffee. Time to take another crack at it.
|
|
Deleted
Deleted Member
Posts: 0
|
Post by Deleted on Nov 23, 2014 7:02:44 GMT -5
Ryan...how big of a hole did you begin with, and how big is it now? Your original picture looks something like a 5/16" or 3/8" hole.
One thing I haven't read on this thread (it might be there, but I missed it) is that it might not actually be you. I've had instances where I was trying to fill a hole or even graft new steel into a tub and what I thought was good steel to weld into was actually that good. It would keep burning up the steel into it finally found strong enough steel.
Out of curiosity, have you drilled a similar hole into a new piece of steel to test?
|
|
|
Post by Ryan_M on Nov 23, 2014 7:13:02 GMT -5
Moose - The original hole was about 3/8". I filled a couple of them without a huge amount of trouble - it's this current one that is giving me fits. I ended up making such a mess of it that I cut out a roughly 2" x 3" section and am now trying to patch that, which is going disastrously. Same mess on attempts to fill a couple of 1/16" holes. I'm just moving them around and/or making them bigger.
The tub is on it's side which means the top of the wheel house that I'm working on is vertical. I'm going to lay the tub flat and try attacking the work area from the top. Not sure if it will make a difference or not but I'm running out of ideas.
|
|
Deleted
Deleted Member
Posts: 0
|
Post by Deleted on Nov 23, 2014 8:29:29 GMT -5
The tub is on it's side which means the top of the wheel house that I'm working on is vertical. I'm going to lay the tub flat and try attacking the work area from the top. Not sure if it will make a difference or not but I'm running out of ideas. Me, too.
|
|
Deleted
Deleted Member
Posts: 0
|
Post by Deleted on Nov 23, 2014 8:33:18 GMT -5
Every welder is different in it's capabilities. You have to get used to the one you have and what it can do. Once you get to use one that works well, you can then know what to look for or expect. If you have any friends that weld near you, take your welder and go weld with his when working well. Then try and adjust yours to do the same. Practice on something besides your Jeep until you feel ready. Oil
|
|
|
Post by athawk11 on Nov 23, 2014 10:19:50 GMT -5
I will add...
For 60 years, the top of the wheel wells have been exposed to much of Mother Nature's wrath. The metal has been blasted clean at some point, so it's likely thinner than the original steel once was. As others are suggesting, this can make welding a nightmare.
Try filling a hole on a side panel where the steel looks thick and crisp. If all works well, then the wheel well surface may just be too thin to fix.
Tim
|
|
|
Post by Ryan_M on Nov 23, 2014 11:13:04 GMT -5
I have pushed the tub and the welder aside for now. I practiced some more on a clean piece of 18ga steel and I can patch drilled holes and weld repairs on that all day long. As soon as I touch the actual Jeep the metal there just evaporates. I've used a full spool of wire and I have less metal on the tub now than when I started. For the sake of my own sanity I'm going to tinker on another part of this project for awhile
|
|
Deleted
Deleted Member
Posts: 0
|
Post by Deleted on Nov 23, 2014 11:43:32 GMT -5
Paper thin metal, poor ground, grounding near to the work site, impurities, heat and feed settings, it takes time to get on to "how to do it". When I mentioned get a weld started on one edge, and work off it's thickness into the repair, stopping before it drops out, I wasn't kidding. Oil
|
|
Deleted
Deleted Member
Posts: 0
|
Post by Deleted on Nov 23, 2014 15:47:00 GMT -5
Lay the tub so your welding horizontal, that's a good share of your problem. Welding verticals is an art in it's self, even more so with a wire feed. I would agree with Tim as well, the original steel is thin to begin with and has been blasted thinner yet. Again welding verticals is a no no, if you have to, start at the top and work down on sheet metal. Haines, the smaller the wire the lower the amperage it takes to run it. With smaller machines it gives you more range as you can raise the amperage and slow down the wire and weld thicker material. I have owned my machine for 25 years and have always run .025, if your machine is less than 200 amps that's all you need IMHO. Our 250 amp at work runs .035, and our 500 amp runs .045 for example for general use, the 500 amp will run much larger wire but limits your range on thinner material, much easier to turn up the wire speed than change to larger wire. Lee 
|
|
|
Post by Haines Garage on Nov 24, 2014 12:18:01 GMT -5
Thanks for the wire explain. Makes sense.
Your gonna laugh, but I am dying to try welding sheet metal again with the stick welder!!
|
|
Deleted
Deleted Member
Posts: 0
|
Post by Deleted on Nov 24, 2014 17:53:04 GMT -5
Thanks for the wire explain. Makes sense. Your gonna laugh, but I am dying to try welding sheet metal again with the stick welder!! When I find time I will send you some rod for that, it will work 
|
|
|
Post by Ryan_M on Nov 24, 2014 21:24:43 GMT -5
I'm not ignoring any of this new advice but welding is still on hold. I will take another crack at it before too long and update accordingly.
|
|
Deleted
Deleted Member
Posts: 0
|
Post by Deleted on Nov 24, 2014 23:54:44 GMT -5
::)I have learned a lot from this thread. I usually weld nothing thinner than 1/8 or 3/16". Welding is not my forte, I have been dragging my feet when it comes to welding on the tub. You guys that know how have real talent, I would like to thank you for sharing your knowledge. I shall tackle my little project with confidence.
|
|
Deleted
Deleted Member
Posts: 0
|
Post by Deleted on Nov 28, 2014 3:31:08 GMT -5
Hi Ryan Here is another suggestion. First of all you bought one of the best welders on the market.
First thing clean both sides of the metal you cannot weld through paint or rust. Second thing clean it again. (Iam sure you got the point)
Check to see if the welder is set up for DCEP, What is DCEP? Is your MIG gun set on the positive side, inside your machine where your drive rolls are? And your ground cable is on the negative side. If not change it. It is easy to do. A lot of welding manufactures send out their machines DCEN. That is were the Mig gun is negative. you don't want that. Make sure machine is unplugged while changing
I hope your using ER70S-6 wire, I like to use .023 wire when welding on sheet metal. Make sure your drive rolls are set to the wire your using. on a Lincoln 140 usually the drive roll will be .023 on one side and .030 on the other. by the way .023 wire is also .024 is the same. You can unbolt the drive rolls and reverse them that is why you see two sets of groves in the drive rolls. if your drive roll is wrong your wire will not feed correctly. There is a black nob with a spring sits on top of your drive rolls this add tension to the wire. when feeding wire though the drive rolls you should tighten the spring tension on the drive roll to not slip. Slowly turn the black tension nob while feeding wire until it doesn't slip then stop turning the tension nob. Unplug machine while changing Drive roll
If you have a farm and your welding a fence use the Flux Core Welding wire. Put the ER70S-6 wire back in the welder!!!!! and use the shielding gas. you did buy the correct gas 75-25 is perfect for MIG welding.
Your shielding gas should have a flow meter. I suggest about 25 to 30 CFH. When you trigger your MIG gun you should here the gas flow. Inert gas bottles have a double seating valve, So when your welding open it all the way to the top. Don't kill it, just open all the way to the stop. After welding turn off the gas!!!!
I would like to explain how other welding process work, It might help to make sense in MIG welding.
On Gas welding you light the torch with the acetylene on and turn the nob until you have a carburizing flame. Then you slowly add the oxygen until you see the flame change to a neutral flame. I know its a quick explanation but you'll get the point. If I hold the torch to close to the metal it will blow a hole or put out the flame. and if I hold the torch to far a way it will not allow me to heat a puddle to weld.
On Stick welding after I strike an arc. If I hold the rod to close to the metal It will blow a hole or will stick the rod. And if I hold it to far a way it will break the arc or not have a quality weld.
The point is, it is absolute the most critical part of Welding. It is called Arc Length. I know I know in MIG welding its called by some Stick out other call it CTWD Contact Tip to Work Distance. This cannot change while welding after you set up the welder.
OK here is where I pull the tail on the cat. Tell my wife that dress makes her look fat. Make a statement no one agree on! Look on the inside lid of your welder that is where your wire is. There is a chart that suggests were to set the welder. It will tell you what gas your using what wire your using and the thickness of the metal your using. Don't use an extension core that is not a heavy duty cord. I never use one that is longer that 25 feet. Now that you have your basic setting set in the machine. Hold the MIG torch so the handle is parallel to the surface your welding. The Nozzle should drag on the surface your welding. (I told you, you would not agree.) THAT IS WHY THE NOZZEL IS INSULATED. By the way the nozzle screws on the MIG torch on a Lincoln welder you should tighten very lightly, two fingers. Because you will be taking off periodically to clean. The contact tip should be recessed in the gas Nozzle about 1/16 of an inch. this is important because while dragging the nozzle and pulling the trigger with one hand your going to adjust the wire speed with the other until you get that frying bacon sound. That is setting your arc length. (this is done on a practice piece of metal.) If the weld isn't hot enough turn up the voltage and set the arc length again. If its to hot turn voltage down and set arc length. (setting arc length is done by turning wire speed while dragging the nozzle while welding until we get that bacon frying sound)
Should I push or pull my weld? How can you push the nozzle if the nozzle is on the metal? Pull your welds. (when you get good you can use other techniques)
Now were going to weld on the Jeep! OK remember we set the arc length on the welder that cant change while we weld on the jeep. The distance we established while practicing or setting the arc length that is the distance were going to weld at. Don't move the nozzle closer or farter away. Make your welds in a series of spot welds ( I know wrong terminology again but you know what I mean. ) Once you make a weld watch it and just before it turns gray make another spot weld and so on until you have made a complete stich weld. When making a spot weld pull the trigger count ONE TWO then stop. you'll get the hang of it. When you get comfortable with welding you can extent that spot weld a little longer. Most technicians do not do continuous welds on vehicle because of warpage. They use a process called stich and skip and it just as it sound.
I hope this will help you SP
|
|
|
Post by Ryan_M on Nov 28, 2014 7:07:00 GMT -5
Very thorough SP, thanks. I believe my setup is correct as it matches everything you describe. That leaves only my technique as the culprit. I may take another crack at it this weekend if I can get the axles finished up and out of the way.
|
|
|
Post by Haines Garage on Nov 28, 2014 8:32:07 GMT -5
Awesome explain on the welder and welding technique. Thanks Sir Jeff!!
|
|
|
Post by Ryan_M on Dec 21, 2014 13:15:17 GMT -5
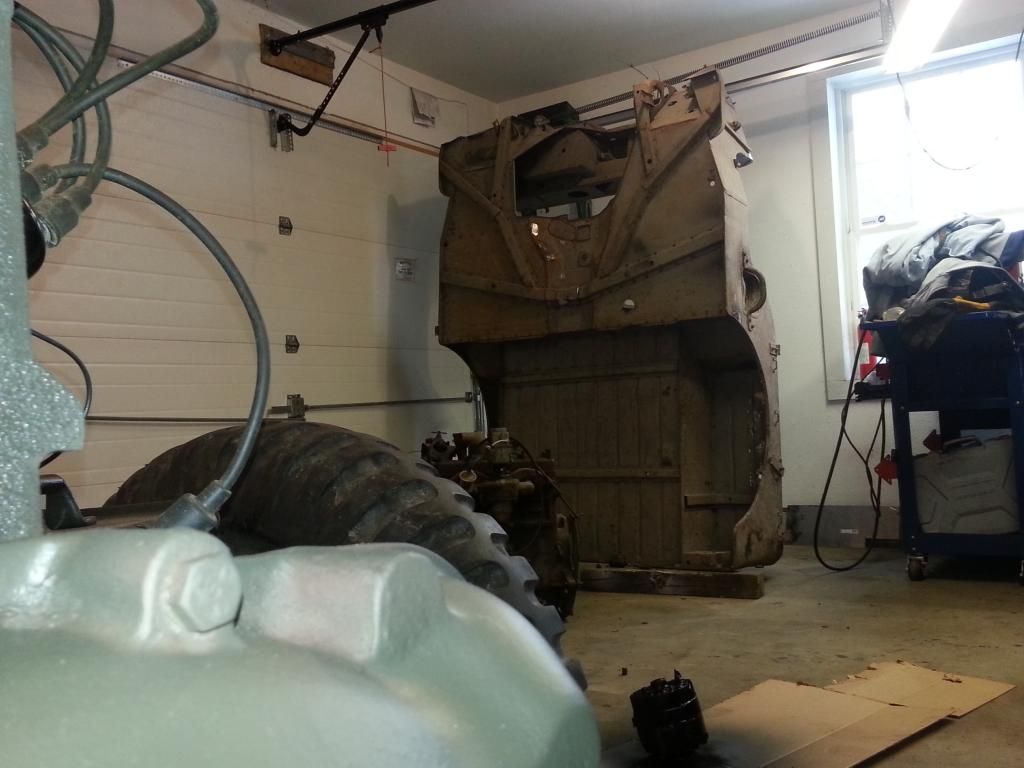 This big fat stupid elephant in the room has been staring at me for weeks while I do my best to ignore it and complete parts of the project that make me feel as though this is hobby is actually rewarding and enjoyable. Enough of this shatty bastage and its ridicule and sneering. Today, I blew the dust off the welder and set to work. Although still pretty ugly, I was able to finally FILL some holes instead of just blow new ones. As butchered as they look, I'll consider it a victory. I did have a friend come over a few weeks ago and give me a couple pointers on technique. I'm just dumb enough that I can read for hours and not get it right but after 2 minutes of actually watching someone do it things begin to click. So here's where I'm at. I've used about 6 miles of wire and a pallet load of flapper discs to fill about 6" square inches worth of holes. What's the best way to finish this out? Any pointers on sculpting those wheel house ridges back to something that remotely resembles their original appearance? What about the uneven pock marks of the welded area? Do I just keep filling and grinding or would it make more sense just to hit that area with a thin coat of body filler? I don't want a bondo queen but how far does one reasonably go with welding before it's "good enough" and filler is OK to use? Regrettably, I'm pretty much neck deep in the learning curve on one of the most visible parts of the entire tub. I'm all in so I have no choice but to ride it out now. This is still a thrasher buggy so I'm very OK if it doesn't look quite "right". If it was a museum piece replacement wheel houses would already be on order but that is not in the cards. I'm chalking this entire tub up to an educational experience. 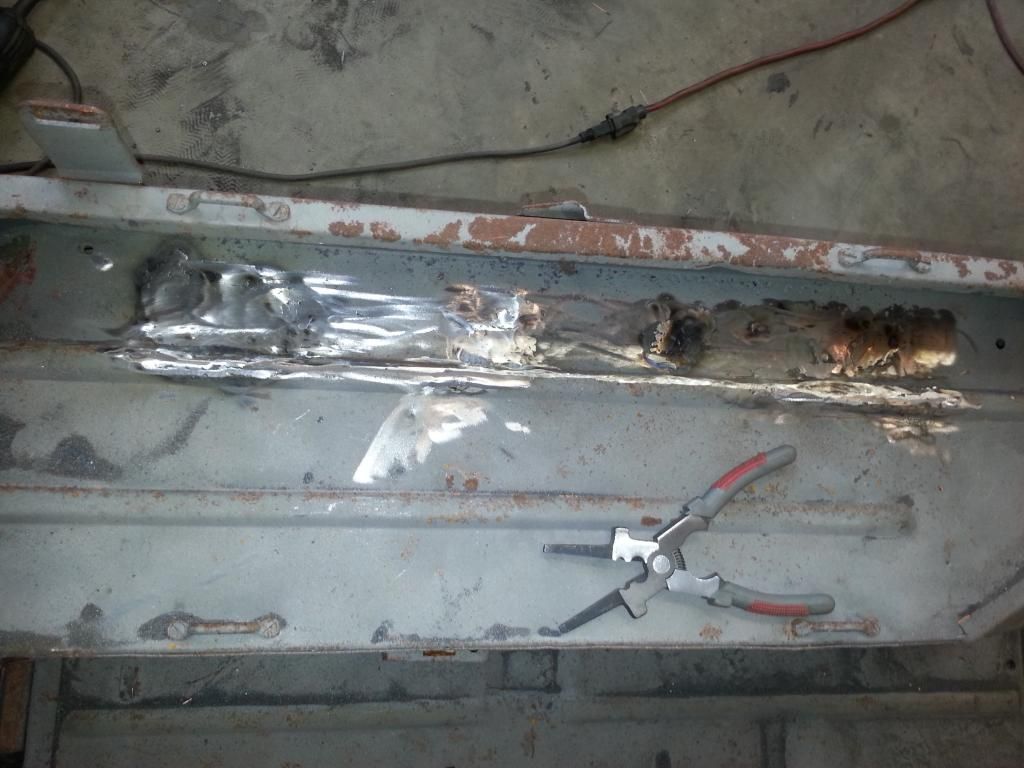 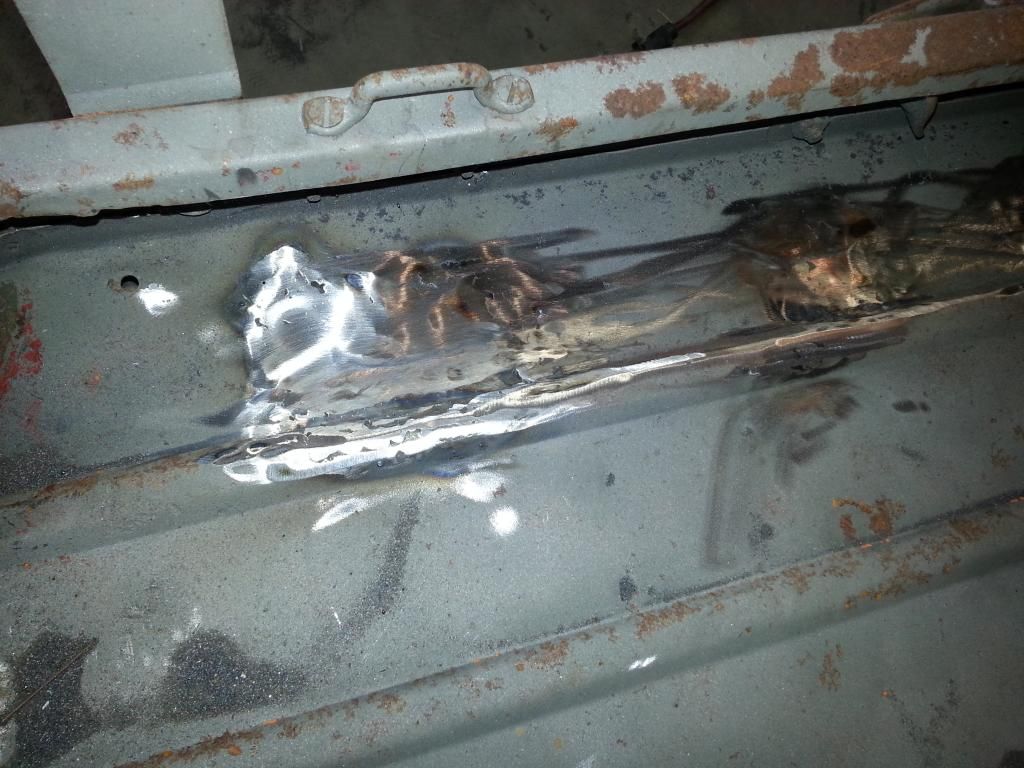
|
|
Deleted
Deleted Member
Posts: 0
|
Post by Deleted on Dec 21, 2014 15:24:42 GMT -5
Grinding is another topic. Even if you have a crappy weld, you can still make it look pretty good by grinding it a certain way or method. If you use a 4 inch grinder, you will work harden it more, and can actually get it so hot it will warp the metal . What I've discovered is a cut off air tool with the 3 inch narrow disc works better. Carefully take the weld down a little at a time and keep the heat down. It cuts fast, and in a smaller area. You can actually put your hand on the grind location soon after you quit. Feel it until you are close to the parent surface. Then quit and change to the 2 inch spin on type 36 grit grinding discs made by 3 M. You can work wonders with it. When it gets worn, you take sissors and cut off the outer 1/4 inch and begin again. Save the smaller ones for tight spots. With the cutoff, you use the thin edge until close, then turn it flat and smooth and even out the weld line before you go to the 2 inch 3M disc. I learned all this from a restoration bodyshop next to me. They cheat and use tig allot, which is a much softer weld than tig. The better you get at it, the less bondo you use. Oil
|
|
|
Post by Haines Garage on Dec 21, 2014 18:05:07 GMT -5
Yes Sir, you look like you are on the right track now. I still am not good at the welding thing. You have definitely improved. You at a point will say.. " Hey this actually is really fun" !
Grinding is a whole other topic could discuss. I like your ideas General.
|
|
|
Post by Ryan_M on Dec 22, 2014 14:03:21 GMT -5
Oil - I picked up a pile of the 36 grit 3M discs and scrounged around to find my air tools and cut off wheels. I should be able to log some serious garage time over the upcoming holiday weekend. I'm excited to try out this new gadgetry.
|
|
|
Post by athawk11 on Dec 22, 2014 15:19:31 GMT -5
Love the photographic angle you chose with the tub standing on end.  Very Ominous!  Tim
|
|
Deleted
Deleted Member
Posts: 0
|
Post by Deleted on Dec 22, 2014 19:10:15 GMT -5
You're going to love those spin on discs by 3M. Spoiled as a matter of fact. I can't live without them now. I keep them in stock. LOL, Oilly
|
|