|
Post by Ryan_M on Nov 21, 2014 19:58:20 GMT -5
I have managed to do nothing but chase holes around my tub for the past two hours. First ever attempt at sheet metal welding is an epic failure. I've tried a variety of settings and even on the lowest ones I'm still blowing holes everywhere. Fill holes - sort of - grind away the 12 pounds of excess slag, weld a little more, blow open the hole, repeat process. If I'm this bad at patching holes there's no way I'll ever be able to cut out a section and then weld in a patch. Everyone I've talked to says how easy this is to get the hang of. What the hell am I doing wrong? 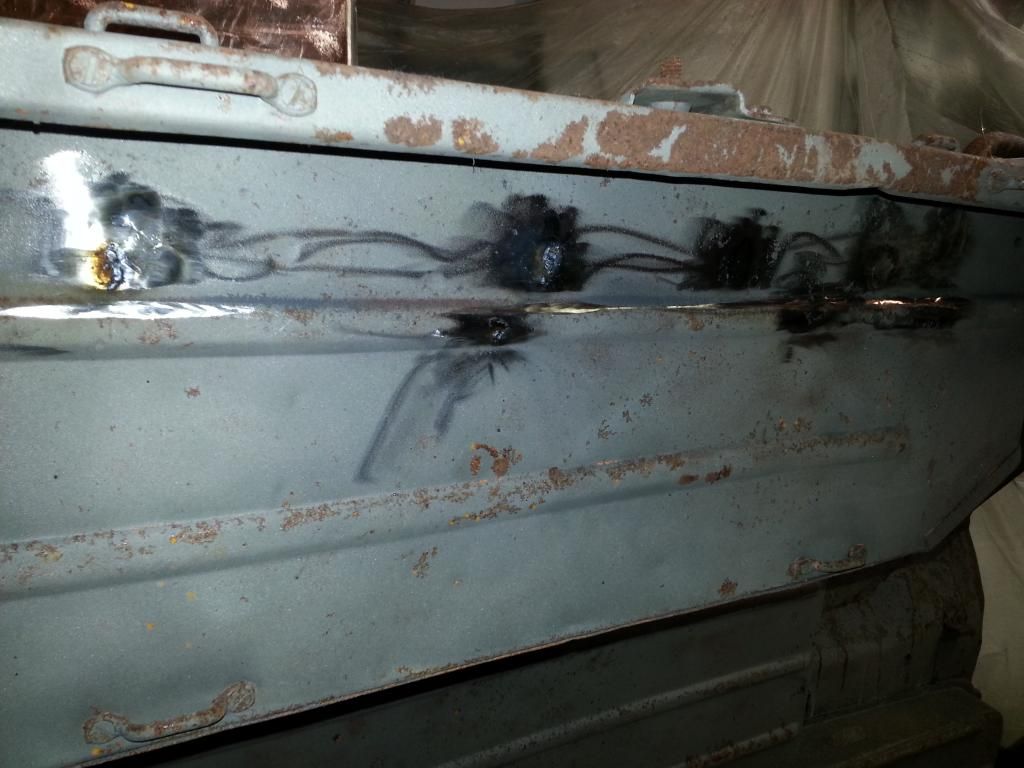
|
|
Deleted
Deleted Member
Posts: 0
|
Post by Deleted on Nov 21, 2014 20:13:42 GMT -5
I'm by far an expert (shut up, p-nut gallery) but when I weld close little holes, I like to put a chunk of something behind the hole to form a backdrop to the weld. The catch is, it has to be something that the weld won't stick to. I think it is aluminum that I use...its a small block of aluminum that I clamp behind the hole. My unit (its mine, HG!) is a cheapo wire flux wire feed deal. Short, rhythmic pulls on the trigger.
Maybe you'll find something in my gibberish.
|
|
|
Post by Ryan_M on Nov 21, 2014 20:32:18 GMT -5
I've been using a piece of copper to back the holes with although it seems to make no difference at all. Maybe I'm not clamping it tight enough? I tried using just short bursts on the gun too - still blowing holes.
|
|
|
Post by zooke581 on Nov 21, 2014 20:47:40 GMT -5
Are you using gas or flux core wire? Flux Core is not very forgiving. When I went to gas the difference and ease of welding was night and day.
|
|
|
Post by Ryan_M on Nov 21, 2014 21:04:27 GMT -5
I went right out and bought gas before I even took the welder out of the box. I've followed every instruction for optimal results and anything I've touched tonight looks worse than when I started.
|
|
|
Post by zooke581 on Nov 21, 2014 21:11:32 GMT -5
Are you holding down on the trigger or are you tapping it? Practice on a piece of similar metal first. And make sure it is clean of paint, rust and any other impurities. And what pressure do you have your gas at? I run mine around 20psi. I did less and my welds were crap.
|
|
Deleted
Deleted Member
Posts: 0
|
Post by Deleted on Nov 21, 2014 21:29:14 GMT -5
Couple questions, when you pull the trigger to weld can you hear the gas coming out of the gun?. what kind of machine do you have and is your wire speed a 4 position switch or a dial ?. a backer is a must, copper is good. Do not think you can "Puddle" the weld on a hole in sheetmetal, short bursts are what your after. In your photo it looks good!  , it looks like your gas is not effective there, but it may be the picture/my bad eyes, LOL. Keep in mind welding is an art that takes time to get onto, you will have days where it goes well, and days where you think you have lost it!. My job comes with lots of welding on thick stuff, I am not a perfect welder but would consider myself above average, and sheetmetal is very humbling to weld. I have an OLD Miller machine that was purposely made for body shops and has some cool features for sheetmetal, like a stitch function where you can set a timer and you simply hold the trigger and it will weld for an instant and stop, on and on, very slick for filling holes. Keep at it, it will get easier  . Lee 
|
|
|
Post by Ryan_M on Nov 21, 2014 22:06:00 GMT -5
OK, discovery of bonehead move. In an act of true desperation I cracked open the instruction book to start reading it (again). I went through it once already but I missed the part about changing the nozzle from the plastic one to the brass one when switching from the out-of-the-box flux core set-up to MIG.
I just spent a few more minutes working and I'm still blowing holes but not nearly as bad. A little practice with this now "correct" configuration and I might actually get somewhere. I need to call it quits tonight on this positive upswing. If I try it for another hour and can't get it I'll never sleep tonight....
And Lee - Lincoln 140 w/ 75/25 mix. Dial wire feed and 4 position amp setting.
|
|
|
Post by Haines Garage on Nov 21, 2014 22:11:38 GMT -5
All have given great advice. I am seriously a novice at best welder. My biggest obstacle was to stop being afraid of the gun, In that I mean, when you first see the SPARK !! It's a little intimidating.
There is no way, and trust me when I say this, you are going to grab this up, like you were born to do so!
Like the members here have told me... Patience and Practice.
The Moose actually showed me how to fill a hole. Go slow, make sure both , surfaces are clean !! Front and back. Clamp that shit tight!!!
You can do it'!!! And I understand your frustration!!!!
|
|
|
Post by Ryan_M on Nov 21, 2014 22:26:38 GMT -5
"Clamp that shit tight!!!"
I think that is also part of the problem - I'm not clamping the brass backer tight enough. The shitty triangle magnets I got at HF aren't strong enough to hold the brass to the steel and I don't have a clamp that will work in the area I need the backer attached. I'm going to have to devise a more creative method. Does the thickness of the brass matter? A thinner piece that would bend to the contour of the subject steel seems like it would also help but it would need to be pretty thin to do that.
|
|
|
Post by Haines Garage on Nov 21, 2014 22:57:01 GMT -5
One more thing I learned... Turn that shit down! The Amps and wire feed. If your burning, maybe your too hot, and wire feed too fast.
Look at me, like I know what I am talking about....
I had the same problem , just started playing with the settings.
|
|
|
Post by Haines Garage on Nov 21, 2014 22:58:31 GMT -5
More comments !!! I am learning this as well!!!
|
|
|
Post by athawk11 on Nov 21, 2014 23:07:53 GMT -5
Ryan,
Sheet metal takes a great deal of patience while learning and while welding. Much different than welding thick metal. You'll eventually wonder what all the fuss was about.
The backer piece doesn't need to be thick. I use a piece of 1" copper pipe that I flattened out. I don't use gas, so the rules may change a bit. Short burst....wait till the molten metal goes dark...short burst...wait till the molten metal goes dark...and so on. When I say "short burst", it's literally about one second. One one thousand...let it cool...one one thousand...let it cool.
The rules will remain the same when you start patching.
Tim
|
|
|
Post by Haines Garage on Nov 21, 2014 23:14:37 GMT -5
Great advice!! Same that was shared with me. Great post Tim!
|
|
|
Post by Haines Garage on Nov 21, 2014 23:16:38 GMT -5
You see the red, and the pool, I think it was Sir Eric who said , once you see that, back off, and stop! Good advice as well.
|
|
Deleted
Deleted Member
Posts: 0
|
Post by Deleted on Nov 22, 2014 7:04:43 GMT -5
"Clamp that shit tight!!!" I think that is also part of the problem - I'm not clamping the brass backer tight enough. The shitty triangle magnets I got at HF aren't strong enough to hold the brass to the steel and I don't have a clamp that will work in the area I need the backer attached. I'm going to have to devise a more creative method. Does the thickness of the brass matter? A thinner piece that would bend to the contour of the subject steel seems like it would also help but it would need to be pretty thin to do that. "Honey...can you put this glove on and hold this block of brass really tightly here? Oh, and close your eyes for a second."
|
|
|
Post by Haines Garage on Nov 22, 2014 15:35:51 GMT -5
[quote "Honey...can you put this glove on and hold this block of brass really tightly here? Oh, and close your eyes for a second."[/quote]
That's funny! I I have not tried that one yet.
She did help me position the rear floor though!
|
|
|
Post by Ryan_M on Nov 22, 2014 17:11:04 GMT -5
This is beyond frustrating. Everything I touch just gets blown apart. Cooper backing, gas at proper level, amp and wire feed at ANY level. All I am doing is burning holes. At this point I wish I had saved the $800 on this welding set-up and just paid someone else to patch the tub, which is what is going to happen if things continue much further at this rate.
|
|
Deleted
Deleted Member
Posts: 0
|
Post by Deleted on Nov 22, 2014 17:20:54 GMT -5
A little practice with your welder first is a good thing to do. Take a piece of the same thickness sheet metal and drill a like hole in it. Then clamp your backer on it. Now play with feed and heat settings until you get the nice bacon frying, steady sound. Use gravity in your favor. I always start with the top and work down on a vertical weld. Get the weld pool or puddle to lay in with good penetration and also get used to stopping when you think it's so hot it will fall out, or burn through and fall. The quicker you learn to do this, the thinner the weld with less grinding needed. If you are in real thin crap or rusty stuff, you learn to get a weld started, and then work forward from it into the weld area. Otherwise it will just fall out and frustrate you. Also, the hotter you get it, the more it pulls and warps. Take your time. Alternate welds in cooler areas. Do not try and weld it solid all at once. When welding in a flat piece you made from a pattern to fix a bad area, get it clamped in and spot it in place making sure it's all even steven. This is butt welding. Then trying not to get it too hot, stitch weld it in cool areas here and there. Stop, let it cool, now grind those welds. Always keeping it as cool as possible . If it warps or pulls, dolly it flat again. Do this over and over until all welded. Do not try and weld it all and then grind. It won't be flat when done. A thin cut off tool type grinder will grind it cooler and faster than a big 3 or 4 inch thick grinder. My method is to first grind with the cutoff tool and quit before you get to the flat surface. You learn to hold it flat just before finishing to level the weld line out. Then I use the 3M 3 inch spin on grinding discs in 36 grit. Those are a gift from God when grinding. Many tricks to this stuff. If you do it well, you have less bondo work later. Bondo work is another topic. More tricks. Oil
|
|
|
Post by Ryan_M on Nov 22, 2014 18:52:27 GMT -5
I'm retiring from welding. To fix a simple 3/8 inch hole that someone had drilled I went from this: 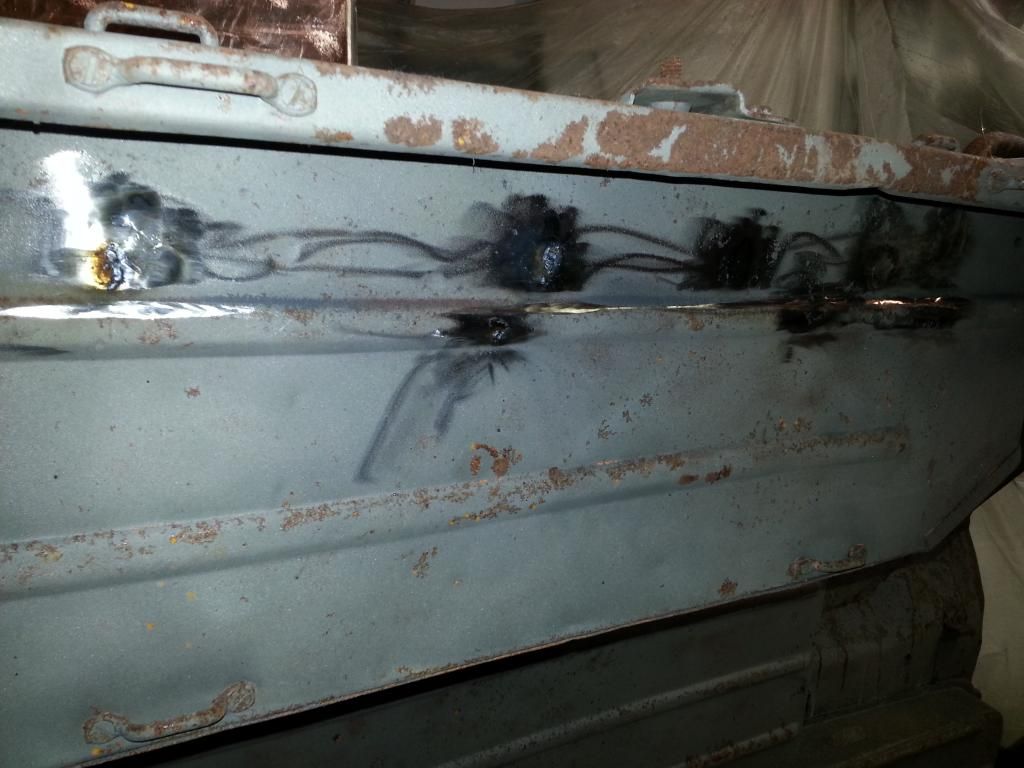 To this: 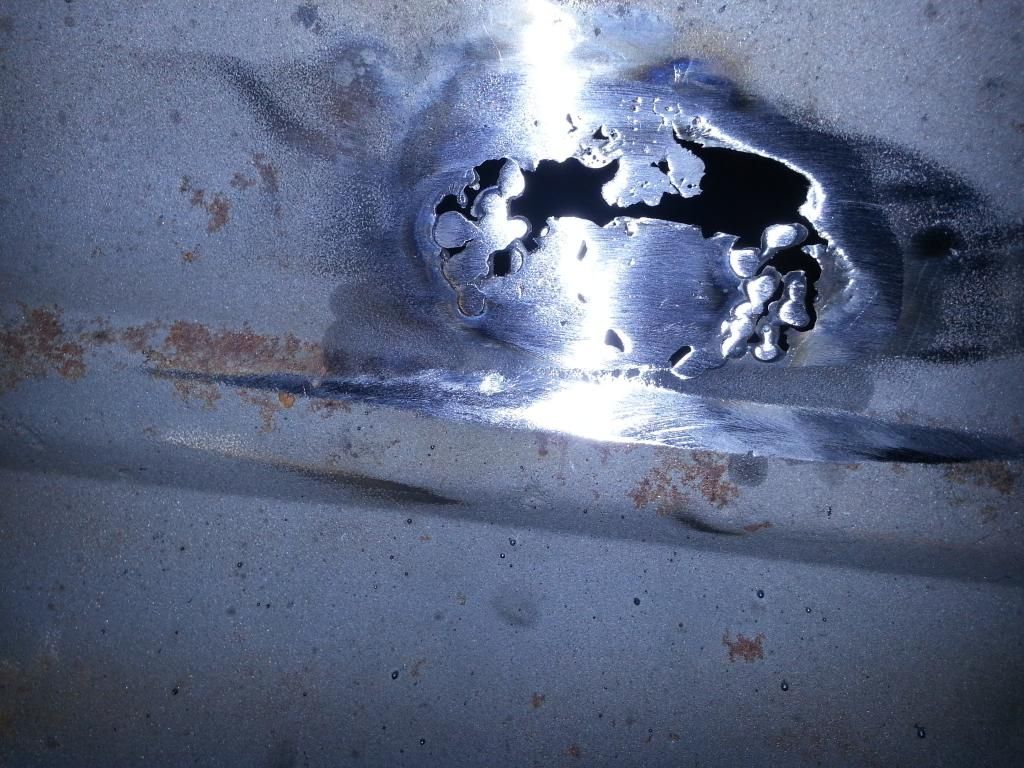 To this: 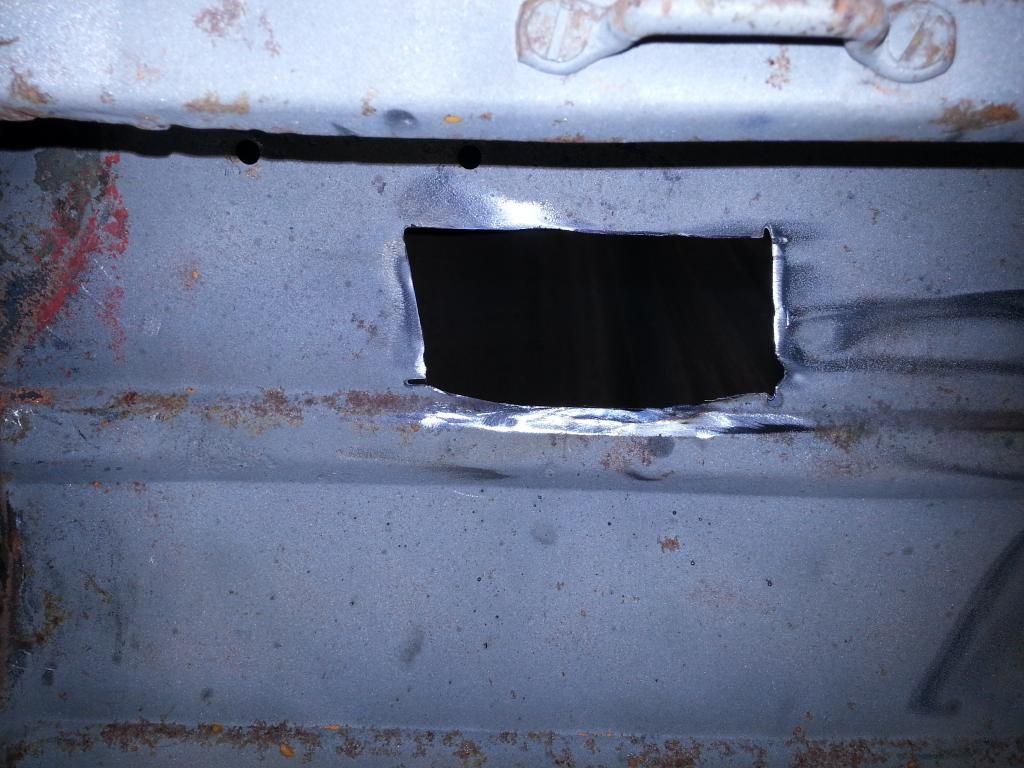 To this: 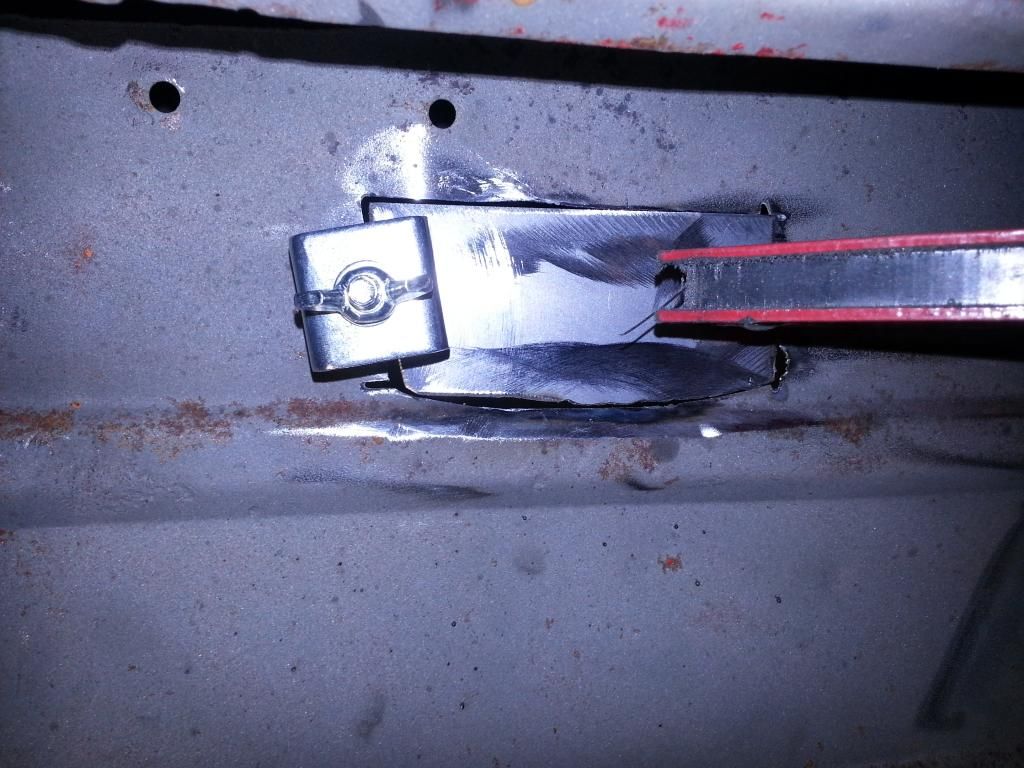 To this: 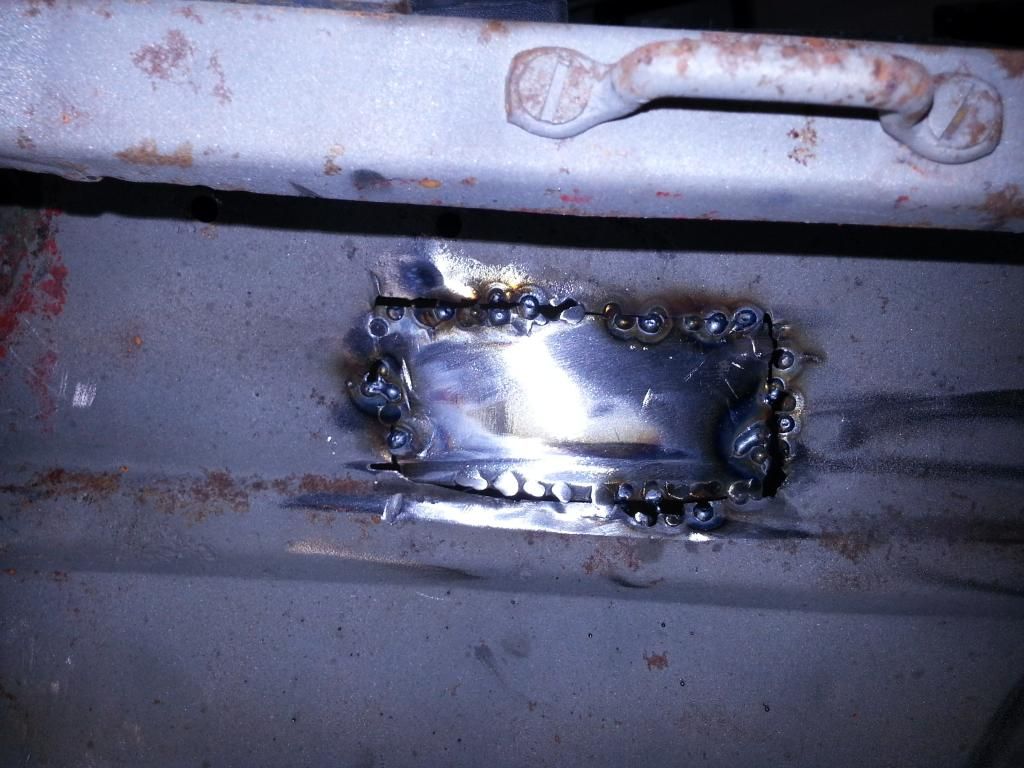 I could spend a year on this tub and it would still be a disaster. I'll find someone else to do it and in the meantime work on the drivetrain. I should have stuck with just painting what was there and running it. Now I've hacked it up so bad I have to have it fixed.
|
|
|
Post by Haines Garage on Nov 22, 2014 19:09:57 GMT -5
No your not!!!' You can do this! You have to clean all the edges your trying to weld. I use a soft pad grinder.
If you give up, you are beaten.. Don't give up!!'
I within the past few months felt the same as you. Then it happens, you have a successful weld! Then holy shit!!!
I am by no means calling myself good, but keep at it! Do what the leaker said. Practice on some other stuff besides your Jeep!
|
|
|
Post by athawk11 on Nov 22, 2014 19:10:01 GMT -5
Ryan,
something is wrong with the set up. Or, How close are you holding the tip to the metal surface?
Before throwing in the towel, let's try something else. Take the gas out of the equation. Get a spool of .35 flux core wire. Make sure you have a .35 tip installed. Set the unit to flux core. Turn your wire feed knob to about 1 to 1.5. Set your amp dial to B. Let about 3/8" of the wire out at the tip before sparking the metal. Keep the tip consistantly 3/8" away from the metal while welding.
Try welding this way and see what happens.
Tim
|
|
|
Post by Ryan_M on Nov 22, 2014 19:23:41 GMT -5
I am holding the tip very close to the work area - 1/4" to 3/8" maybe? If I pull it away I get that horrible "SNAP CRACKLE POP" sound which almost always blows a bigger hole. Holding it close makes the nice "sizzle" sound.
I did cut a square out of a brand new piece of 18ga steel and then welded it back in to place. I blew holes at first but quickly got the hang of it and finished it out pretty nicely. On the trigger for a second, let it cool, move, then back on the trigger. Laying a long flat bead on that same new steel is a thing of beauty.
I will swap over to flux core now just to see how much damage I can do with that.
|
|
|
Post by Haines Garage on Nov 22, 2014 19:25:16 GMT -5
Ryan, something is wrong with the set up. Or, How close are you holding the tip to the metal surface? Before throwing in the towel, let's try something else. Take the gas out of the equation. Get a spool of .35 flux core wire. Make sure you have a .35 tip installed. Set the unit to flux core. Turn your wire feed knob to about 1 to 1.5. Set your amp dial to B. Let about 3/8" of the wire out at the tip before sparking the metal. Keep the tip consistantly 3/8" away from the metal while welding. Try welding this way and see what happens. Tim That's sound advice!! Try it! Your not quitting....No Sir!!
|
|
|
Post by Haines Garage on Nov 22, 2014 19:28:28 GMT -5
I am holding the tip very close to the work area - 1/4" to 3/8" maybe? If I pull it away I get that horrible "SNAP CRACKLE POP" sound which almost always blows a bigger hole. Holding it close makes the nice "sizzle" sound. I did cut a square out of a brand new piece of 18ga steel and then welded it back in to place. I blew holes at first but quickly got the hang of it and finished it out pretty nicely. On the trigger for a second, let it cool, move, then back on the trigger. Laying a long flat bead on that same new steel is a thing of beauty. I will swap over to flux core now just to see how much damage I can do with that. There you go!!! And clean off all paint rust, etc!!! Now, as this thread goes on , I can't wait to hear the...I did it!!! If you look back, you will see I said the same things you did. Believe!!! That's another one! I believe you can do it, now you have to.
|
|