|
Post by Haines Garage on May 6, 2014 20:06:35 GMT -5
I am starting this thread for that fact that my knowledge of welding is very limited. I have been a home improvement contractor for over 20 years, and am no stranger to tools. I have twisted wrenches for much longer than that. The welding thing has never really made sense to me. I have no reason why. Seeing the skills that both Sir Hawk ridge, and Sir Eric have shown on this forum, I thought maybe it appropriate for a thread on welding skills and techniques. Here's the kicker...look back into the tools thread here. That is my Grandfathers Welder, that I want to use. I also have a MIG, and a Harris Torch set. If you gentleman would be so kind, please start with some basics.
|
|
Deleted
Deleted Member
Posts: 0
|
Post by Deleted on May 6, 2014 20:51:05 GMT -5
arc welding, practice, also clean metal means a happy weld.
|
|
|
Post by Haines Garage on May 6, 2014 20:55:56 GMT -5
arc welding, practice, also clean metal means a happy weld. OK ...Lets start with this two 1/4 inch pieces of flat stock. walk me through a simple weld to join them together.
|
|
|
Post by Haines Garage on May 6, 2014 21:23:39 GMT -5
arc welding, practice, also clean metal means a happy weld. Also definition of arc welding... And yes, I am serious.
|
|
|
Post by athawk11 on May 6, 2014 22:02:13 GMT -5
Welding is a hard thing to describe with words. It's sort of a 'feel' 'site' and 'sound' kind of skill. I use a small, but nice wire feed with fluxed wire. Simple to use, but you need to practice to get good at it. A good self darkening helmet is a must have. Welding a couple 1/4" chunks together with my set up... Amps turned up. Wire feed rate turned up a bit. Slow arc motion. Back and forth in a half moon movement. Watch your molten metal flow, not your spark. You want to almost 'dip' your stick or wire back into the molten metal. If you move too fast, you won't get good penetration, and it will sound sparky. You want to hear a smooth crackly buzz sound. If you move too slow, your weld will glob up on you. You want to slightly melt the two pieces of metal. If you aren't melting the metal, you need to turn up the amps more or slow down your movement. I'm reading back on this and sort of laughing at myself. I'm all over the place. Again, it's hard to describe welding.  Sheet metal welding is a whole different approach. God help you my friend. I can't tell you how many holes I burned, or poor penetration welds I had to do over, while learning to weld sheet metal. I'm pretty good at it now, but there was a large learning curve to overcome. I spent hours repairing my repairs. Tim
|
|
|
Post by zooke581 on May 6, 2014 22:11:06 GMT -5
I am with you athawk11. It is hard to describe. I do it by feel and practice. I watch videos and go from there. The sound of bacon is what helps me out. When you welding sounds like crisp bacon frying you are pretty much there. But welding like metals as a test before you weld what you want is best. I also turn it up a notch when welding a thinner part to a thicker part.
I have had no classes on this, I just jumped in with both feet.
|
|
|
Post by Haines Garage on May 7, 2014 7:22:23 GMT -5
Video's great idea. I will check YouTube out, and post some here. This is going to be fun...
|
|
|
Post by Haines Garage on May 7, 2014 7:25:41 GMT -5
Also, there is a method to my madness with this thread. I am hoping that it goes from the basics to actual Flat Fender Jeep specific application.
|
|
|
Post by Haines Garage on May 7, 2014 17:22:01 GMT -5
Found some cool ones.
That one was shown to GE employees..Grandpa was a GE employee in Schenectady, NY
That's for starters
|
|
Deleted
Deleted Member
Posts: 0
|
Post by Deleted on May 7, 2014 19:43:44 GMT -5
MHO, we can pump rainbows of welding philosophy where Bo stuck the draglink all day and it will not make you a better welder  , practice makes perfect!. MIG, I prefer gas with it, flux core wire is dirty, great for sheetmetal work. Arc or stick welding, if you have an AC machine, 6013 rod is the standard, 6011 is the deep penetration rod good for root passes, would not be my choice for sheetmetal work, but with very fine rod it can be done. If you have a DC machine  , 7018 rod is the professional choice. Gas welding with an acetylene torch is good for sheetmetal, takes much time to learn, I like it. TIG welding is much like gas welding only with an electric arc, very controllable, an excellent choice for sheetmetal, but the cost for a home hobbyist is on the hi side. An old friend once told me, "If your not comfortable when welding or cutting, your work will show that!", very true, so make sure your work is well placed, and plan ahead. Lee 
|
|
Deleted
Deleted Member
Posts: 0
|
Post by Deleted on May 7, 2014 22:38:35 GMT -5
MHO, we can pump rainbows of welding philosophy where Bo stuck the draglink all day and it will not make you a better welder  , practice makes perfect!. MIG, I prefer gas with it, flux core wire is dirty, great for sheetmetal work. Arc or stick welding, if you have an AC machine, 6013 rod is the standard, 6011 is the deep penetration rod good for root passes, would not be my choice for sheetmetal work, but with very fine rod it can be done. If you have a DC machine  , 7018 rod is the professional choice. Gas welding with an acetylene torch is good for sheetmetal, takes much time to learn, I like it. TIG welding is much like gas welding only with an electric arc, very controllable, an excellent choice for sheetmetal, but the cost for a home hobbyist is on the hi side. An old friend once told me, "If your not comfortable when welding or cutting, your work will show that!", very true, so make sure your work is well placed, and plan ahead. Lee  X2!!!! The videos are good for learning theory, but practice, practice, practice! It's the only way you'll learn how much heat to use, how the angle of the torch/ rod effects puddle formation and penetration, where you want to weld on different joints to have equal penetration on both parts, etc. MIG is the easiest to learn, the most popular for the hobbyist and the easiest to use on sheet metal. I prefer shielding gas over flux core, but you can't use shielding gas where there is a breeze of any sort. The down side to mig is initial cost, (but you already have one) and you can lay the prettiest beads and not have any real penetration, if your not careful. That being said, I personally haven't used a mig in ten years, so I'm sure welder technology has changed a little bit. IMHO, (yes, I'm a opinionated S.O.B, lol) your Monkey Ward AC/DC is one of the most versatile style of machines there are. Here's my current machine, old as the hills, but a goody! 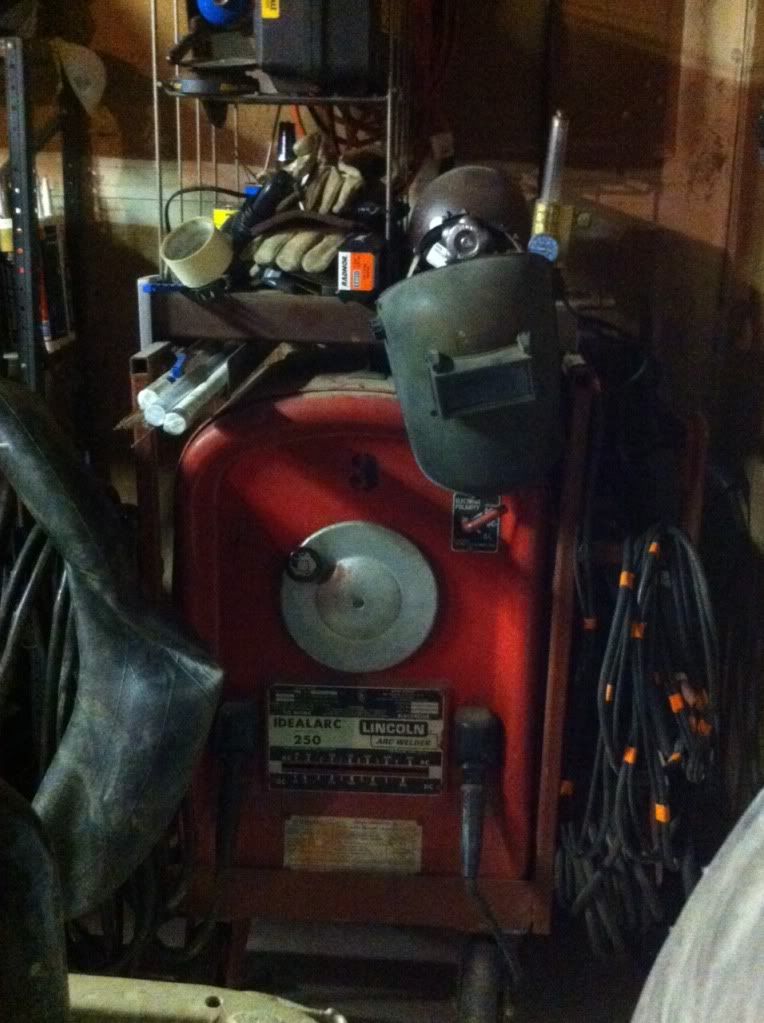 (I talked my old job in to surplusing it when they laid me off awhile back, hehe) On thin stuff and stainless steel, I use DC straight and a TIG rig, although, I'm no sheet metal artist like Sir Tim and Sir Eric, it does real good. On other stuff I use a 1/8" or 3/32" 6011, known around here as the "farmer's rod", or a 1/8" 7018 on DC reverse, usually with a 6011 root pass. As Lee said, the 7018 had more penetration, and it seems to be less brittle so to speak, it works real good on trailer frames and such. On really thin stuff, such as pin holes in air cleaner cups, I'll braze it, love brazing! I hope this helps! I'm no professional welder, I taught myself the very basics when I was 13, learned more in high school, working etc, I've never regretted it! Btw, I had a cheap auto change welding helmet years ago, burnt my eyes with it, threw the pos away and been using a regular hood with a #10 lens since. So If you use a auto lens, be sure is a decent one. In case you don't know, if you do burn your eyes, you won't realize it until about 2 o'clock in the morning, when you wake up with the feeling that your head is on fire. The only way I know to get relief is to cut up some potatoes, wrap them in a paper towel and place it over your eyes. Kinda homegrown I know, but it seems to work!!! Not trying to scare you, but some things are best known in advance.... So Sir Schiller, go buy some rods, scrounge some scrap metal, strap the helmet on your bean and go to town!!! You will figure it out!! Trust me!!!
|
|
|
Post by Haines Garage on May 8, 2014 17:09:48 GMT -5
Thanks for the replies my friends...This will grow into a great thread. I just know it with all the talent here!
|
|
|
Post by Haines Garage on May 8, 2014 17:31:46 GMT -5
|
|
Deleted
Deleted Member
Posts: 0
|
Post by Deleted on May 8, 2014 19:28:38 GMT -5
Cool videos! What is not on YouTube these days...... Working with a oxyacetylene rig is FUN! With a can of flux, you can weld with baler wire in a pinch if you need too!! How you set the flame is critical. A neutral flame (where the inner "feather" mentioned in the video just disappears) is what you want, but it seems you can get away with a slightly carbonizing (rich) flame for brazing, and a slightly oxidizing (lean) flame for welding. For instance, This a front wheel bearing nut socket I brazed a few years ago, still going strong, and almost free. 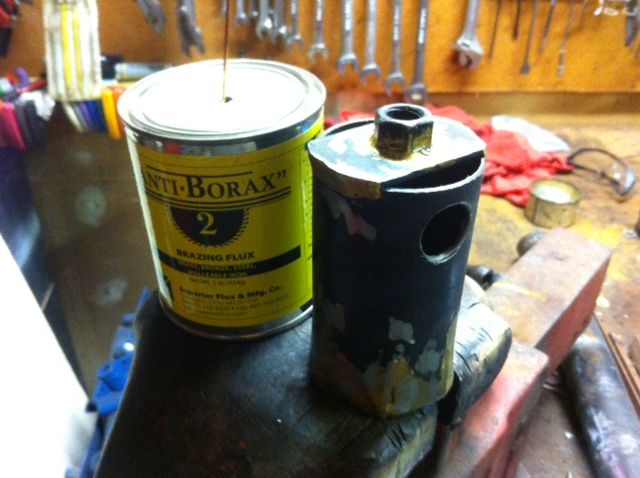 Post Correction: Last year I went to a #9 shaded lens and a 1.25 power magnification lens in my hood. Still don't need glasses yet..... but a little help makes a difference!! 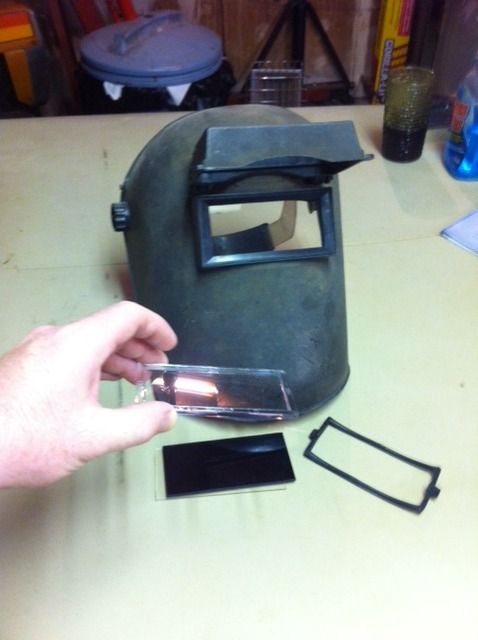
|
|
|
Post by zooke581 on May 8, 2014 20:55:44 GMT -5
Gee, you guys give me far more credit than I deserve. I just learned gas welding in the last two months when I started this tub. I have never done it before. Just been using flux core for the last 10 years and minimal at that. But I have to say it sure is fun. And I get better on each piece I do. I do practice on scraps when I am not sure before I got to actual part.
|
|
Deleted
Deleted Member
Posts: 0
|
Post by Deleted on May 9, 2014 0:03:05 GMT -5
if your arc welding always pull the puddle never ever push it. you also don't have to weave just do a straight line 15 degree angle to lead your weld and straight up and down for the other angle. use some 6013 to learn it has way more slag on top so it will look better and help you learn 6011 is kinda a pain to weld and 7018 is good for structure. the first numbers are breaking strength min so if your doing a trailer or something important use 70xx not 60xx if your doing your tub 60xx. use DC for all your arc welding it is simpler and easier. get some 3/16 cut off plates about 5 inches long and use a full 6013 rod to make a padding plate. the full rod should take you about its length minus 2 inches or 3 inches to travel that plate. anything more or less and your to fast or slow. always chip away from yourself with a slag hammer and at the 3/16 plate run 85 amps for the sides right on the edge and 100 ish for the rest. alternate which way you pull per line and build up one bead right on top of the next so at the end you build up the whole plate pretty smoothly. (so pull a bead then chip and quench the plate, then put the center of your rod on the edge of that last bead and pull the opposite direction. repeat until finished).
|
|
Deleted
Deleted Member
Posts: 0
|
Post by Deleted on May 9, 2014 0:07:09 GMT -5
oh and height of the rod above the work piece, if you see flames your to high if your arc is really dark your to low. a good rule of thumb is for the diameter of the rod you should be that high above the work piece.
|
|
|
Post by Haines Garage on May 9, 2014 15:48:51 GMT -5
Once again Sir Schimmster...you have most impressed me. I read your post twice, and will remember what you said... Thank you!
|
|
|
Post by Weld Leaker on May 11, 2014 6:25:20 GMT -5
I've had the privilege to work next to a restoration body shop that has been in the business of welding up older cars for 40 years. Boy have I seen some interesting techniques. Gas welding, leading, Tig, and Mig . They mostly use Tig and Mig. Stick or Arc welding is mainly used for heavy deep penetration welds on thick stuff. A good mig with argon gas shield will do such a nice clean job . It will repair a huge variety of things from frames to thin sheet metal. There are techniques to fitting welding, and holding the metal . One thing you learn is that metal crawls all over with heat. You need to tie it down , hold it from moving, or go at it in a gentle planned matter expecting it to react to the welding you are doing. Mig welds are much harder to grind clean than tig. Tig is the same hardness as the surrounding metal when done and is a dream to grind. Tig is like arc gas welding. You strike a electric arc and then feed wire into the weld pool. Harder to do than mig. Gravity is your friend or enemy. Mig is easier to do things like vertical or overhead welds. Warpage and pulling of the metal due to welding is what botches up the job. You learn to control it and keep it to a minimum with technique. You learn to plan out your welds so grinding access is there, or use tools like hole punches that make plug welding similar to spot welding. You learn to test fit things and hold with sheet metal screws and clamps in preparation to welding it. Your goal is to repair a area back to it's original shape and fit without applying too much body filler. Body filler is "leveling compound". " Fender in a can". Production body work: " cave it and pave it". I was once told I need a floor polisher to cut and buff my quality paint jobs----------LOL. A bunch of comedians next to me. Oh I almost forgot-------the art of shrinking metal back into itself. That could be another topic here! Now, I'll move to the guest human test and sign out. See how I sacrifice for you guys! Signed Oil Guest
|
|
|
Post by Haines Garage on May 26, 2014 10:20:58 GMT -5
Sir Moose is coming by this afternoon to teach me his mad skills!
|
|
Deleted
Deleted Member
Posts: 0
|
Post by Deleted on May 26, 2014 22:53:57 GMT -5
keep the fire extinguisher handy
|
|
|
Post by Haines Garage on May 27, 2014 18:22:06 GMT -5
keep the fire extinguisher handy Good Advice, And I also bought and use the Fire Mat! 
|
|
Deleted
Deleted Member
Posts: 0
|
Post by Deleted on Jun 24, 2014 6:18:07 GMT -5
Just to throw this in there, I am relatively new to welding sheet metal but I have found that when I, do a butt weld, I have more success if I put a piece of brass or copper behind the seam. This helps to keep the two sheets flush with each other, helps to dissipate heat from the weld and helps to keep your weld from blowing through. Since brass and copper are non ferrous metals, the weld will not stick to it. Very good for filing in un wanted holes or joining two metals where there is a large gap.
Sorry if I'm telling you something that you already knew.
|
|
Deleted
Deleted Member
Posts: 0
|
Post by Deleted on Jun 24, 2014 18:53:33 GMT -5
Just to throw this in there, I am relatively new to welding sheet metal but I have found that when I, do a butt weld, I have more success if I put a piece of brass or copper behind the seam. This helps to keep the two sheets flush with each other, helps to dissipate heat from the weld and helps to keep your weld from blowing through. Since brass and copper are non ferrous metals, the weld will not stick to it. Very good for filing in un wanted holes or joining two metals where there is a large gap. Sorry if I'm telling you something that you already knew. Excellent tip, I will try this!  , thanks for posting  Lee 
|
|
Deleted
Deleted Member
Posts: 0
|
Post by Deleted on Jun 24, 2014 19:26:00 GMT -5
Funny...I've always done this when welding up the Bubba holes, but never thought about it when welding sheet metal panels together. Brilliant!
|
|